Cleaning Furnace For Polymer Processing Tools
Difficult to clean materials are removed from metal tooling in a safe, quick and reliable operation. Suitable for plastic molding, pellet manufacturing, electric wire and rubber manufacturing operations. Customers have high praise for TABATA’s CLEAN SHOT cleaning furnace, with over 500 units sold worldwide.
TABATA’s CLEAN SHOT is good for cleaning polymer processing tools, from breaker plates to screws.
CLEAN SHOT ※Demo units are available.
"CLEAN SHOT" is comprised of a carbonizing furnace and air blasting system. Polymers are burned off in a sealed furnace, preventing smoke emissions during the process. Residual is removed using an air-blast sprayer.
Features
● Short working time
Working with the air blast device performed by the operator's hands can be completed in about 2 to 5 minutes, even in complex shapes.
● Even complex shapes can be handled
Even in the interior of thin, long holes and bent holes, and complicated shaped parts that we cannot clean by brushes and instruments, fine particle beads are very effective for deep cleaning.
● Temperature control to avoid damage from heat
Since the treatment temperature of the carbonization furnace can be freely set up to the maximum 600℃, it can reduce the influence on parts.
● Safe to use and environmentally friendly
Since it is not a combustion method, it hardly releases harmful substances into the atmosphere. Residues generated after removal can be disposed of as general industrial waste.
● Equipment is compact and easy to handle
Flue gas duct facilities are not required. Simply connect the power supply and dry air and you can use it immediately.
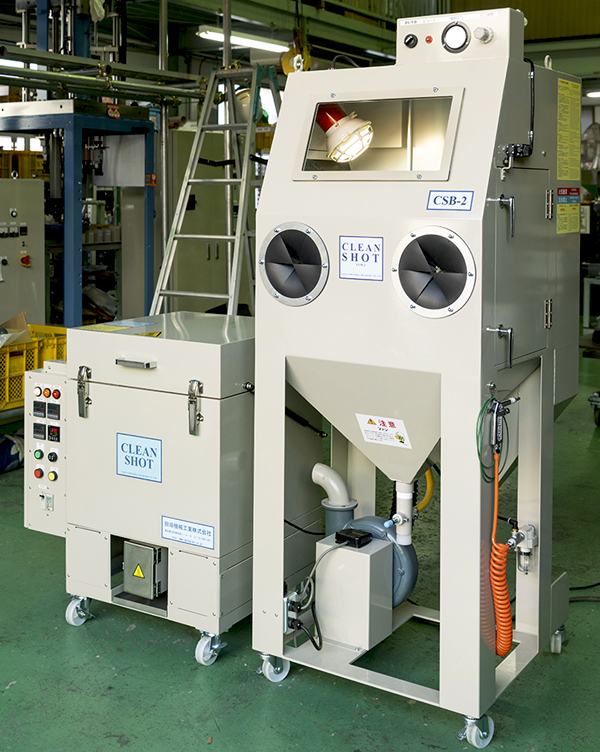
Item | |
---|---|
Equipment Configuration | Carbonizing Furnace |
Air blast device | |
Carbonization treatment | Heat treatment under trace oxygen ⇒ Polymer dissolution ⇒ Collection tray (flow drop) ⇒ Residual carbonized film |
Air blasting unit | Residual carbonization coating ⇒ Short-time cleaning and removal |
Applicable parts | Breaker plate, dies, screws, etc. |
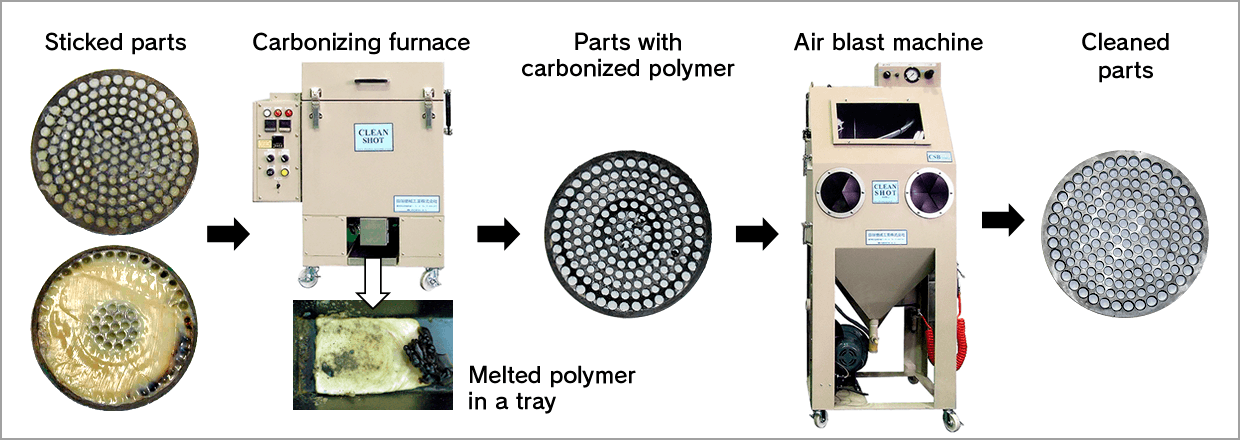
Carbonization furnace standard specifications
Items | Unit | Specification | |
---|---|---|---|
TYPEー2/250 | Outer size | mm | W575 × D575 × H908 |
Effective size | mm | W250 × D250 × H180 | |
Heating method | ー | Electrothermal heater | |
Power supply | V | AC200 | |
Heater capacity | kW | 2.1 | |
TYPEー2/400 | Outer size | mm | W800 × D575 × H908 |
Effective size | mm | W400 × D250 × H180 | |
Heating method | ー | Electrothermal heater | |
Power supply | V | AC200 | |
Heater capacity | kW | 3.3 | |
TYPEー2/550 | Outer size | mm | W950 × D575 × H908 |
Effective size | mm | W550 × D250 × H180 | |
Heating method | ー | Electrothermal heater | |
Power supply | V | AC200 | |
Heater capacity | kW | 4.1 | |
TYPEー2/700 | Outer size | mm | W1100 × D575 × H908 |
Effective size | mm | W700 × D250 × H180 | |
Heating method | ー | Electrothermal heater | |
Power supply | V | AC200 | |
Heater capacity | kW | 4.79 |
●There is demonstration machine "TYPE-2/250".
Air blasting equipment standard specifications
Items | Unit | Specifications | |
---|---|---|---|
CSBー1 | Body size | mm | W510 × D800 × H1267 |
Front door size | mm | W450 × D253 | |
Injection method | ー | Direct-pressure system | |
Box size | mm | W450 × D350 × H388 | |
Nozzle | mm | φ2 | |
Air consumption | m³/min | 0.1 | |
Total Drive Power | kW | 1.05 (AC100V) | |
Standard abrasive | ー | Glass beads | |
Accessory equipment | ー | Dust collector | |
CSBー2 | Body size | mm | W650 × D700 × H1777 |
Side door size | mm | W360 × D480 both left and right | |
Injection method | ー | Suction abrasive material circulation method | |
Box size | mm | W650 × D500 × H700 | |
Nozzle | mm | φ6 ceramic | |
Air consumption | m³/min | 0.5 | |
Total Drive Power | kW | 0.211 (AC100V) | |
Standard abrasive | ー | Glass beads | |
Accessory equipment | ー | Dust collector (bag filter), etc. | |
CSBー3 | Body size | mm | W800 × D950 × H2285 |
Front door size | mm | W650 × D650 | |
Injection method | ー | Suction abrasive material circulation method | |
Box size | mm | W800 × D650 × H800 | |
Nozzle | mm | φ6 ceramic | |
Air consumption | m³/min | 0.5 | |
Total Drive Power | kW | 0.411 (AC200V) | |
Standard abrasive | ー | Glass beads | |
Accessory equipment | ー | Dust collector (bag filter) Cyclone separator, etc. |
●There is demonstration machine "CSB-2".
Example of removing adhesive polymer by Clean Shot
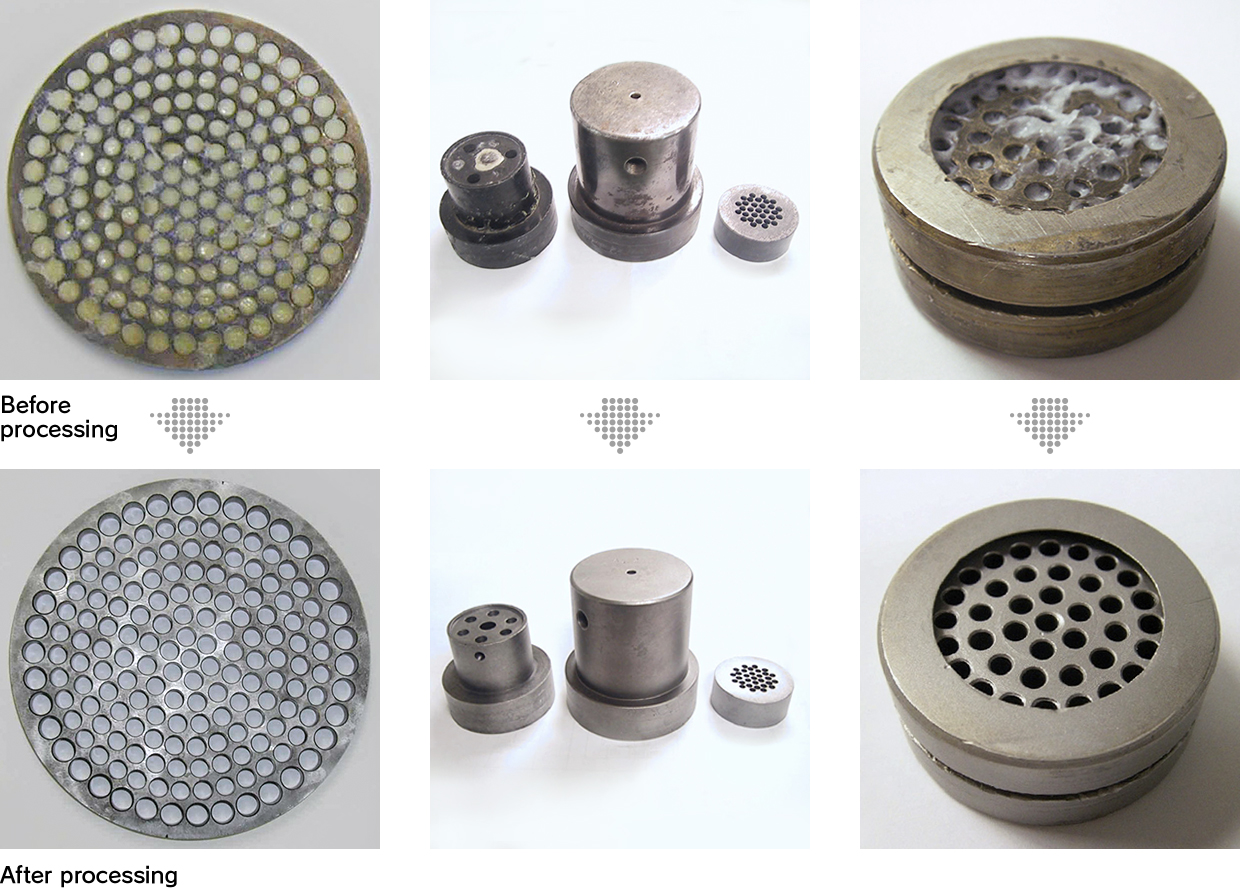
※In addition to the above dimensions, we will also design and manufacture them according to the cleaning parts.
Cleaning Equipment For Screw
Individual design to fit screw dimensions.
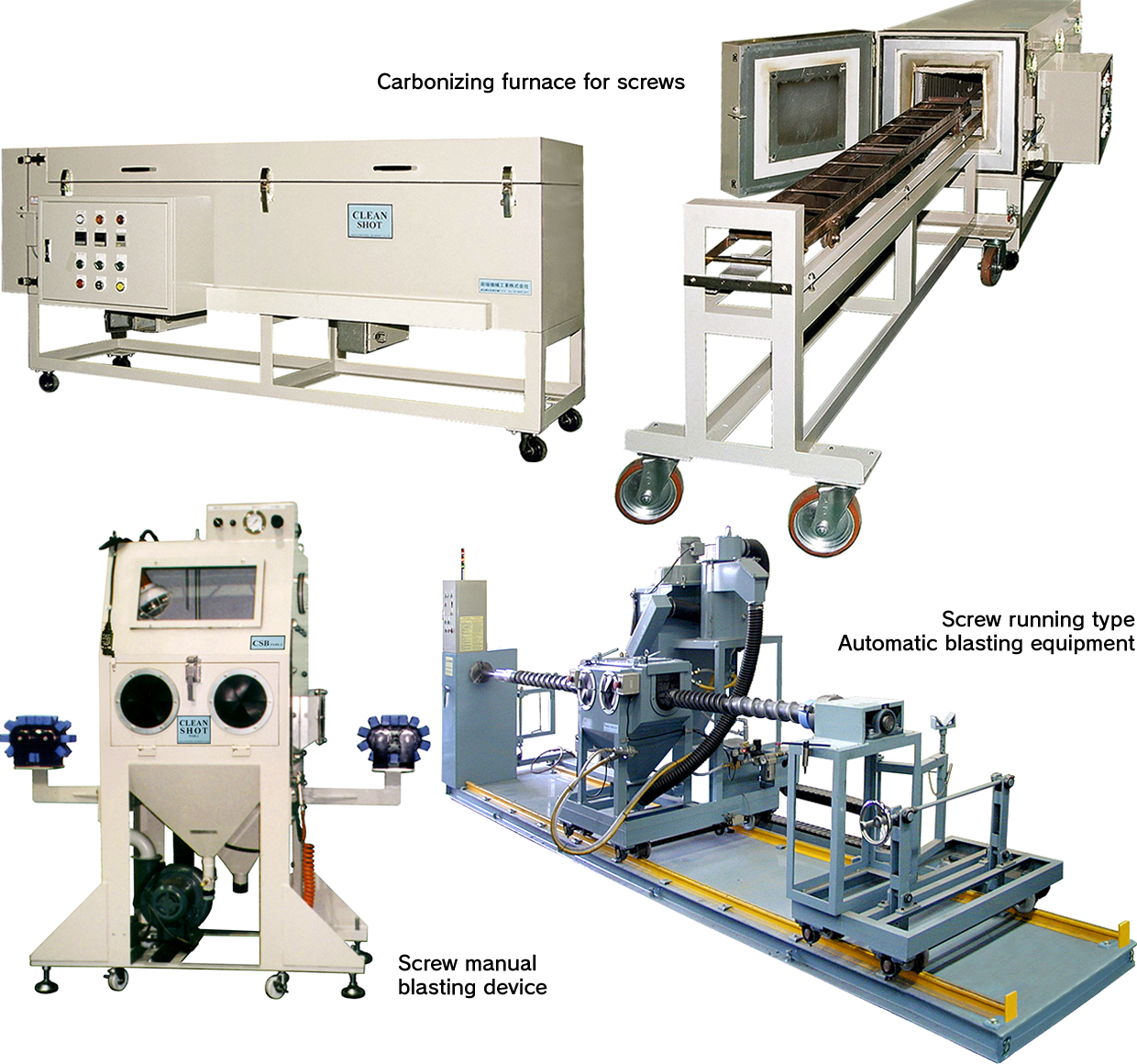
Direct Pressure Blasting Equipment
Our "Clean Shot" has hundreds of experiences in parts cleaning for plastic processing machinery, such as screws, breaker plates, nozzles, dies, etc. By utilizing those experiences, we made a non-heating type blast cleaning equipment. This equipment is ideal for parts cleaning to remove polymers such as fluorinated resins and PVC which generate strong corrosive gases when heated.
Features
● Operability
Set the target parts in the blast box and put abrasive material into the pressurized tank. Push the foot pedal and spray the cleaning material from the nozzle to the work. Operation is as simple as pressing the pedal.
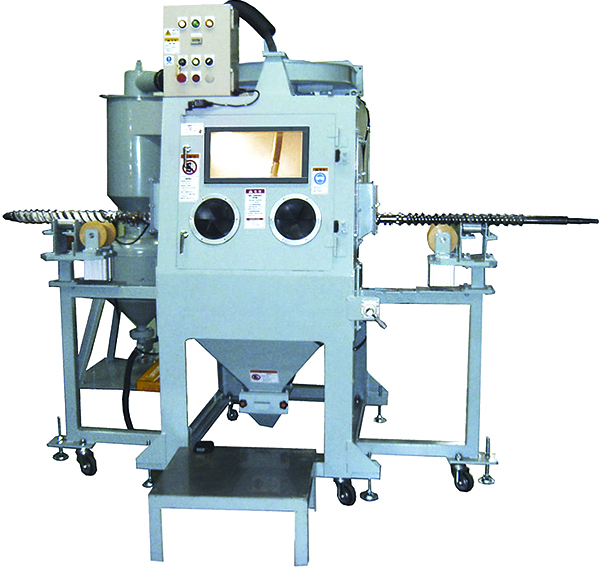
Direct pressure circulation type
(compatible with small screws)
DMAB-104
● Space saving
This is a compact structure in which the dust collector is integrated, so it does not take up any space.
● Safety
Since it is injected in the blast box, the abrasive material does not scatter. In addition, as the process is performed at room temperature, the target parts will not be deteriorated by heat. The abrasive is made of plastics and pressures are as low as 0.5MPa, so there is no risk of plating peeling or damaged components.
● Economical efficiency
The injected abrasive material is circulated for reuse. Since the abrasive material automatically returns to the pressurized tank, the working time for the abrasive material filling can be reduced.
Processing process
・Spray abrasive material from the nozzle and peel off the polymer sticking to the workpiece with the impact.
・The peeled polymer and the abrasive are automatically separated in the apparatus. The collected abrasive material is returned to the pressurized tank for reuse.
・The peeled polymer and the fine abrasive are supplemented by the included dust collector and trap.
Items | Unit | Specifications |
---|---|---|
Machine dimensions | mm | W2160 × D2320 × H2500 |
Electrical capacity used | kW | 0.95 (excluding compressor) |
Nozzle Diameter | mm | 5 |
Air consumption | Nm³/min | 1.3 Pressure 0.49MPa (full dry air) |
Pressurized Tanks Capacity | Liter | 50 |
Abrasive | ー | Soft abrasive (standard is plastic) |